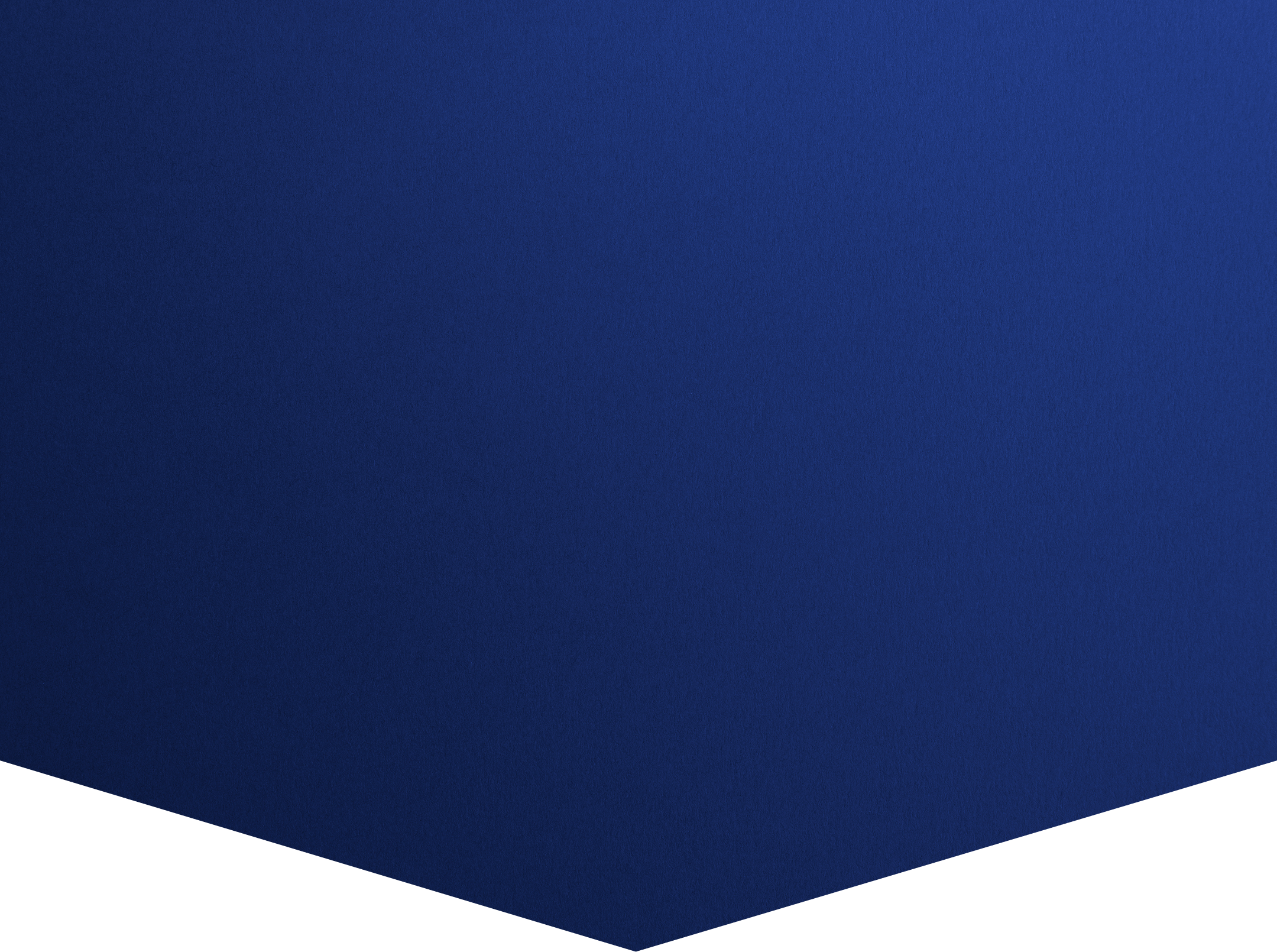
An ISO & CE Compliance Company
About Us
Manufacturers and
Exporters of High-Quality
BFS Machines & Moulds
V S Pharmatech is committed to providing high-quality products and services related to BLOW FILL SEAL TECHNOLOGY systems. We specialize in BFS MACHINES & MOULDS for LARGE & SMALL VOLUME PARENTERALS:
- Known for providing best-in-class products and services.
- Committed to providing in-time delivery.
- Best understands the requirement of users.
Our BFS Machines
Material of Construction
- 1.Machine Frame: SS304
- 2.Safety Panels & Locking Units: SS304
- 3.Filling Unit & Filling Nozzles: SS316L
- 4.CIP/SIP, Product Contact Pipes: SS316L
- 5.All such parts with Product contact: SS316L
- 6.All such parts with NO Product contact: SS304
- 7.Moulds: Aluminium Bronze
- 8.PLC Siemens S7 / Scada system
- 9.Servo System
- 10.Servos Hydraulic System
- 11.Filters
- 12.Parison Head: HDS Hardened
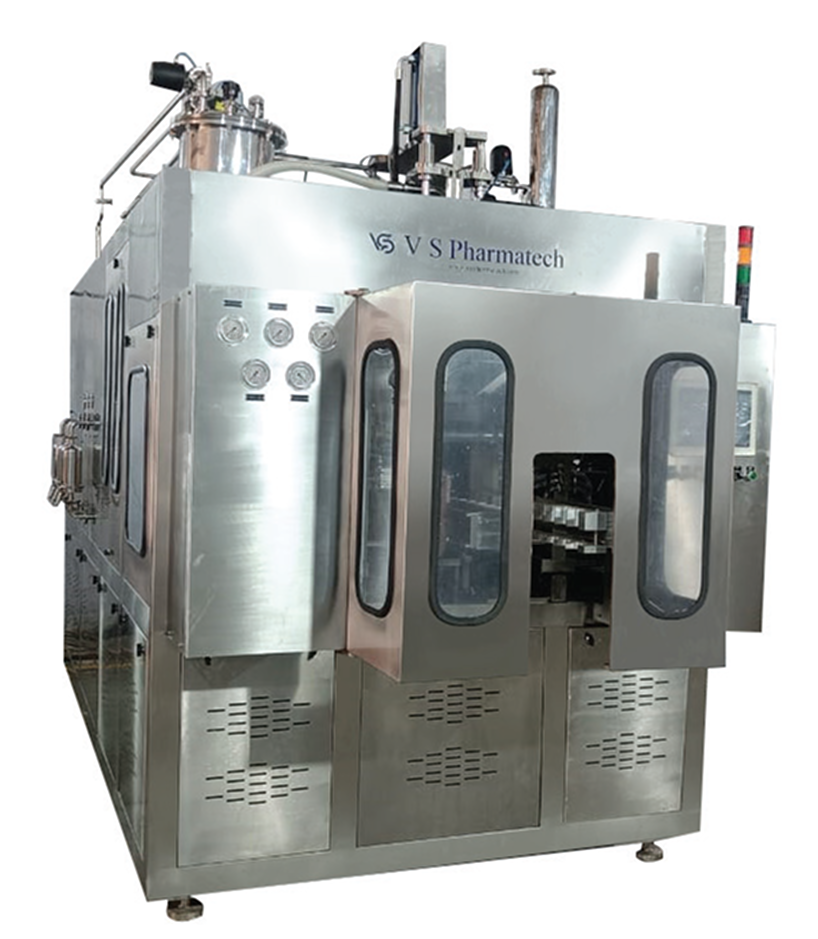
Experience
0+Projects Completed
0+Works Employed
0+Projects Running
0+Our Services
Maximize the potential of your BFS Technology
At VS Pharmatech, we pride ourselves on delivering not only high-quality Blow-Fill-Seal (BFS) machines and moulds but also a comprehensive suite of services designed to support your manufacturing operations. Our expertise ensures that your systems run smoothly, efficiently, and reliably throughout their lifecycle.
Machine Refurbishment & Upgradations
We specialize in upgrading and refurbishing BFS machines of any make or model to extend their operational life and enhance performance.
Diagnostics & Technical Assistance
Our advanced HMI and SCADA systems enable remote monitoring & diagnostics, allowing us to quickly address issues and optimize performance.
Annual Maintenance Contracts (AMC's)
Our AMC plans ensure your machines receive regular maintenance & dedicated expert attention, keeping them in peak condition, extending their lifespan.
Machine Installation and Training
We provide end-to-end support to get your BFS machines installed and equip you with the essential skills to operate & maintain BFS machines effectively.
Our Streamlined BFS Process
From container formation to sealing, our Blow-Fill-Seal technology ensures unmatched quality in aseptic manufacturing.
Extrusion
Plastic granules are melted and formed into a hot hollow pipe of molten plastic (parison).
Blow
The parison is enclosed in a mould, and sterile compressed air shapes it into the desired container.
Fill
Liquid product is sterilely filled into the formed containers using sterile filling nozzles.
Seal
The top of the container is hermetically sealed, ensuring product sterility and tamper resistance.
De-flashing
Excess material (flash) is trimmed away, leaving a perfectly formed, ready-to-use container.
Salient Features
Innovative Features That Define our Excellence
Our BFS systems combine advanced engineering and practical design to redefine the standards of aseptic manufacturing.
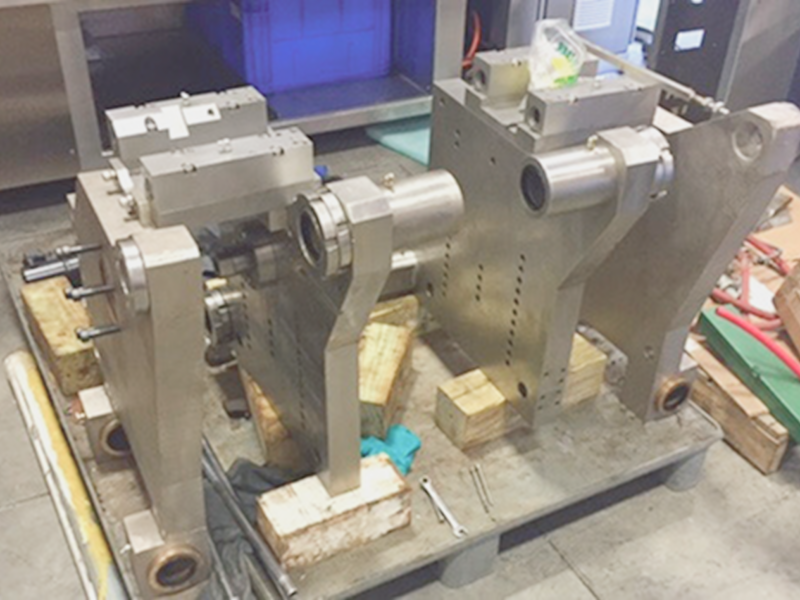
Mould Carriage
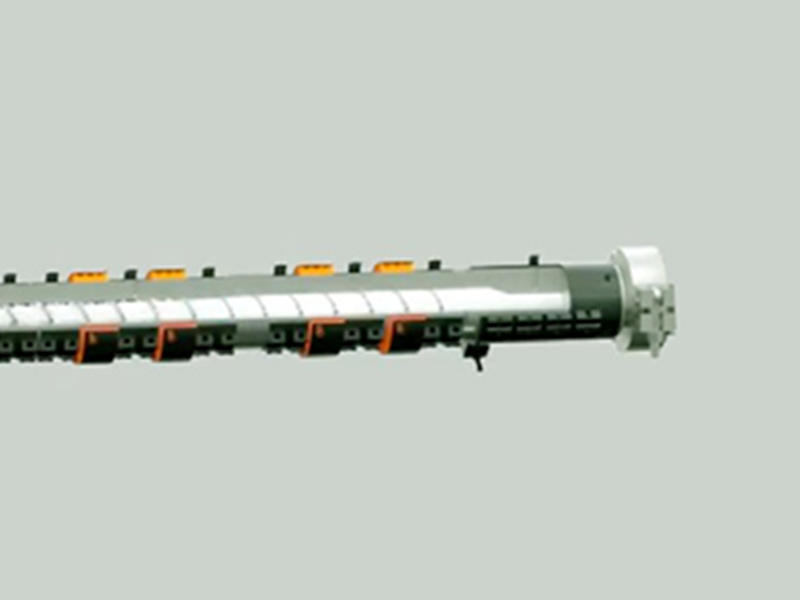
Extruder Head
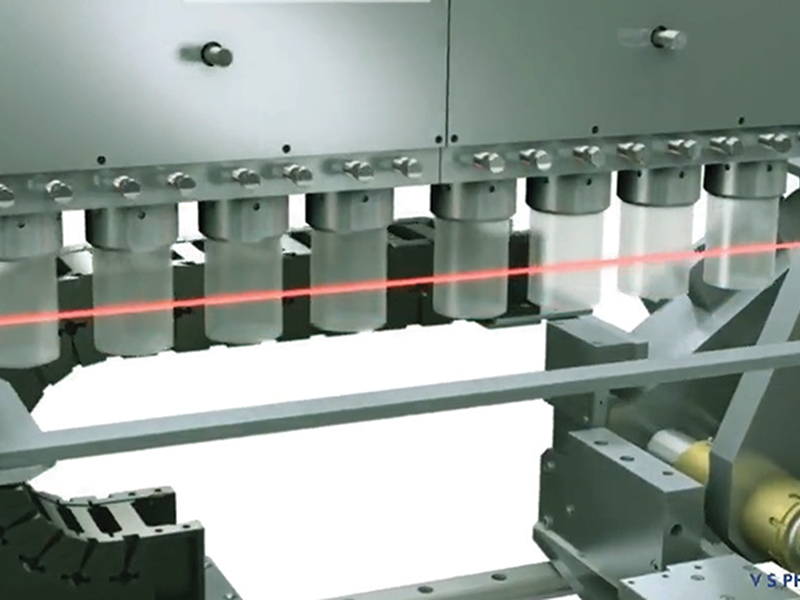
Hot Knife Cutting Device
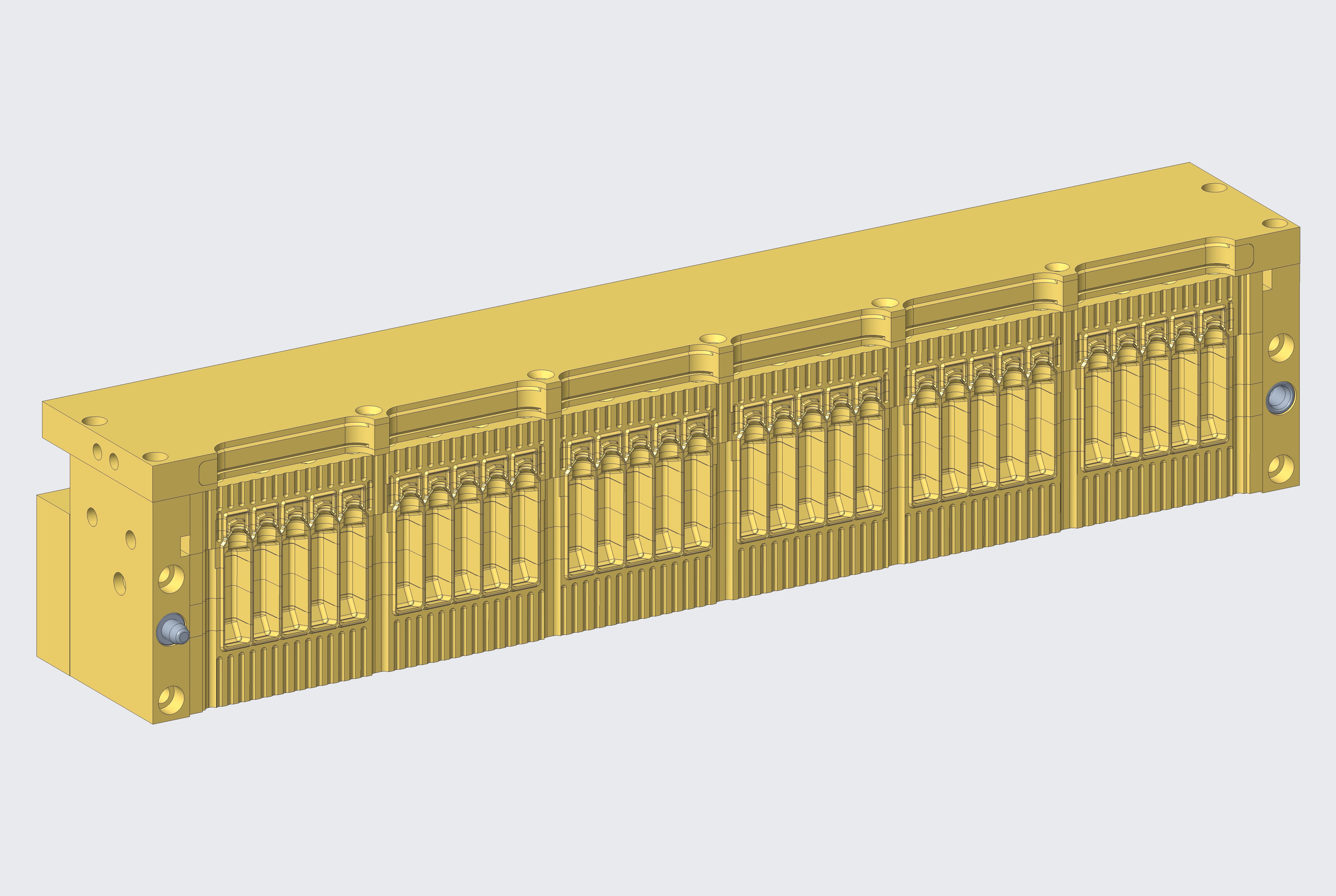
SVP Mould
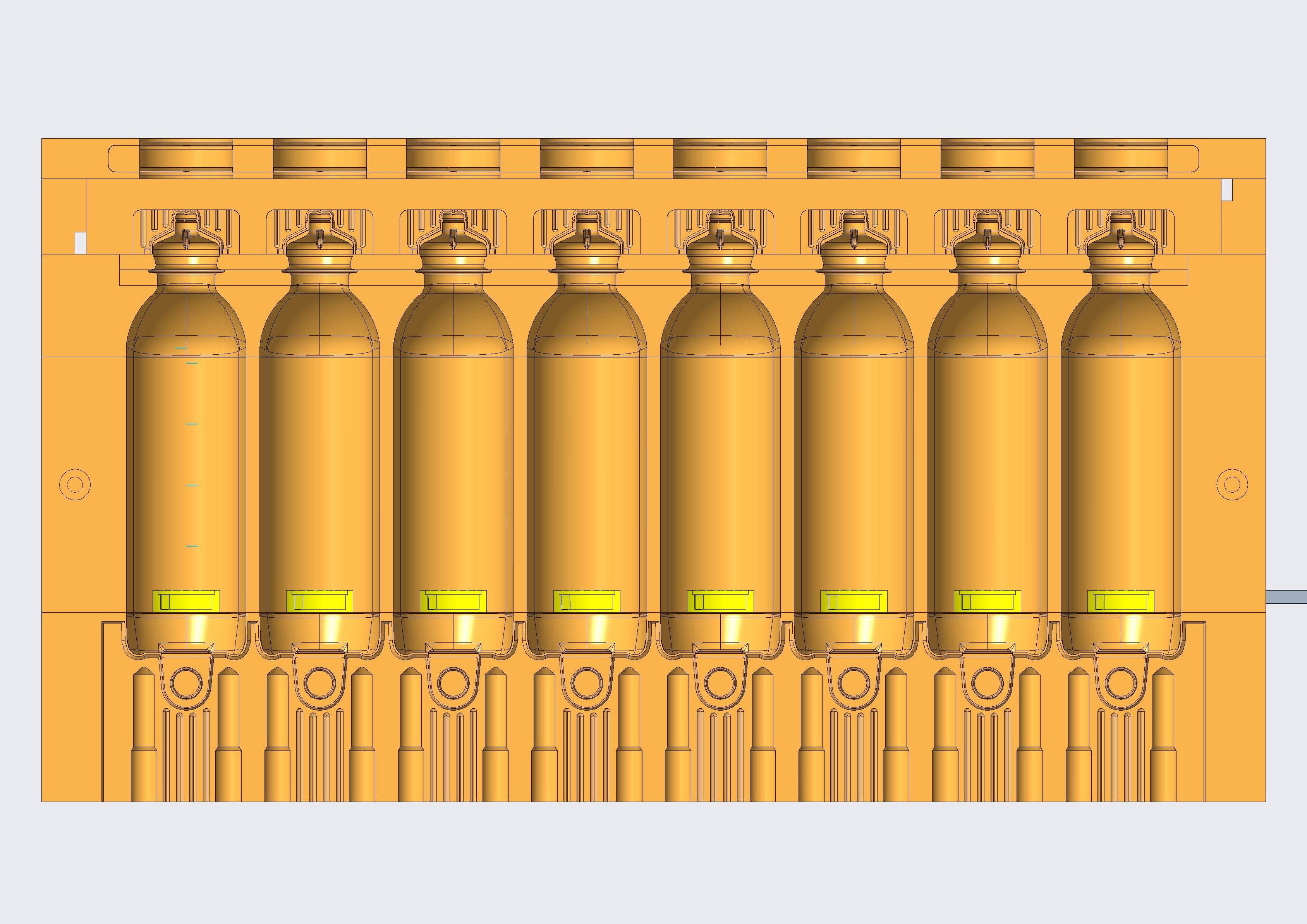
LVP Mould
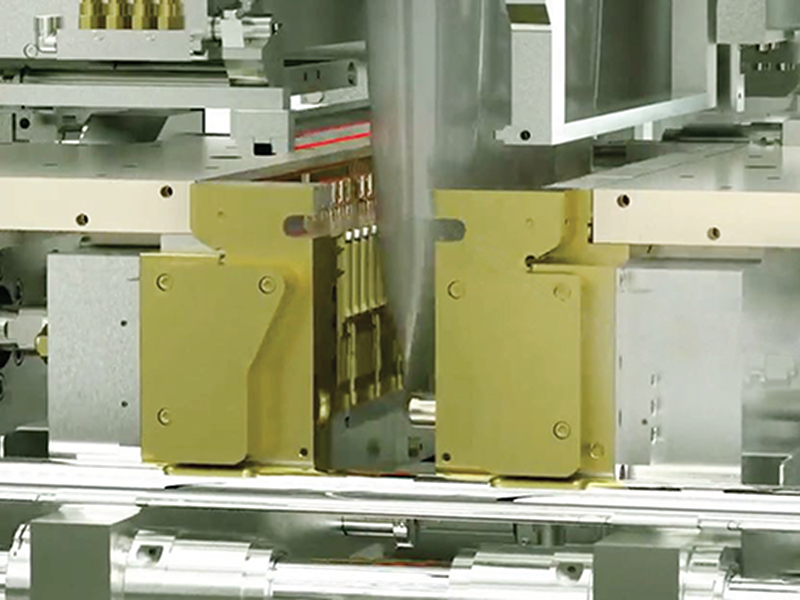
Mould Closing Unit
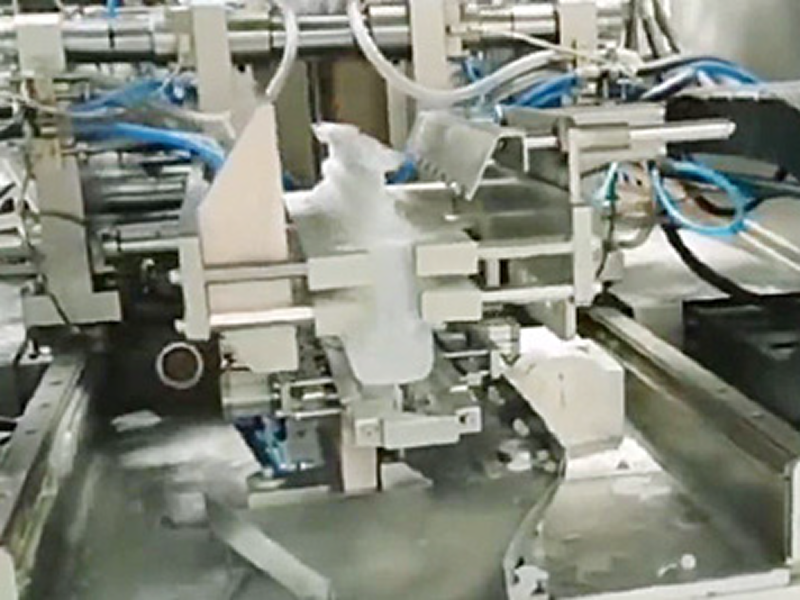
Automatic De-flashing System
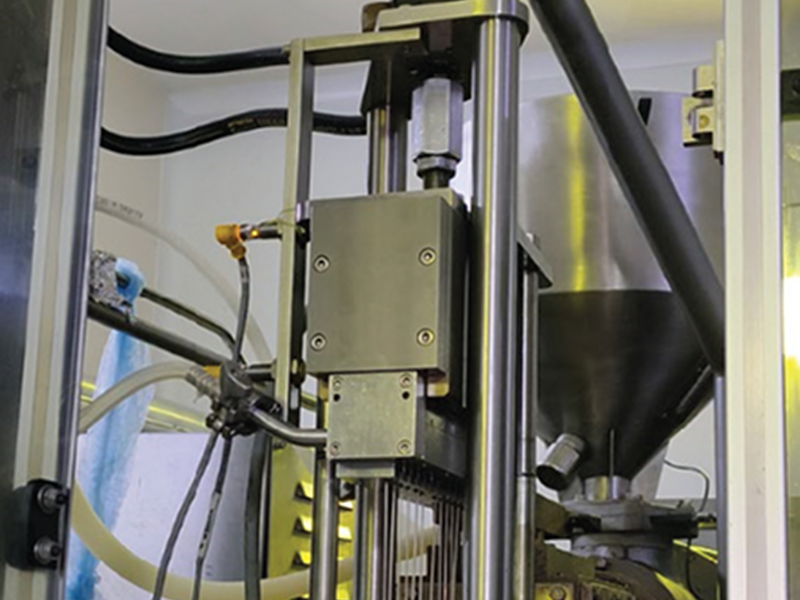
Filing Unit Assembly
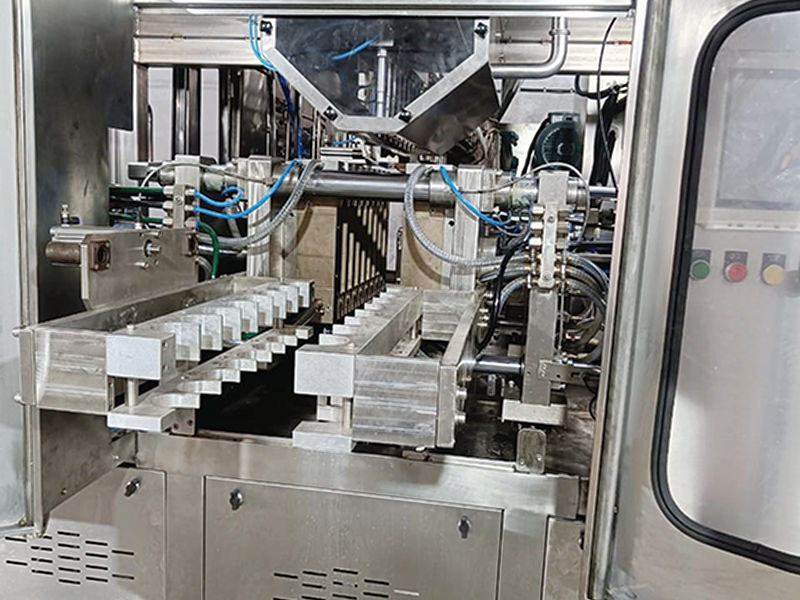
Time Pressure Dosing System
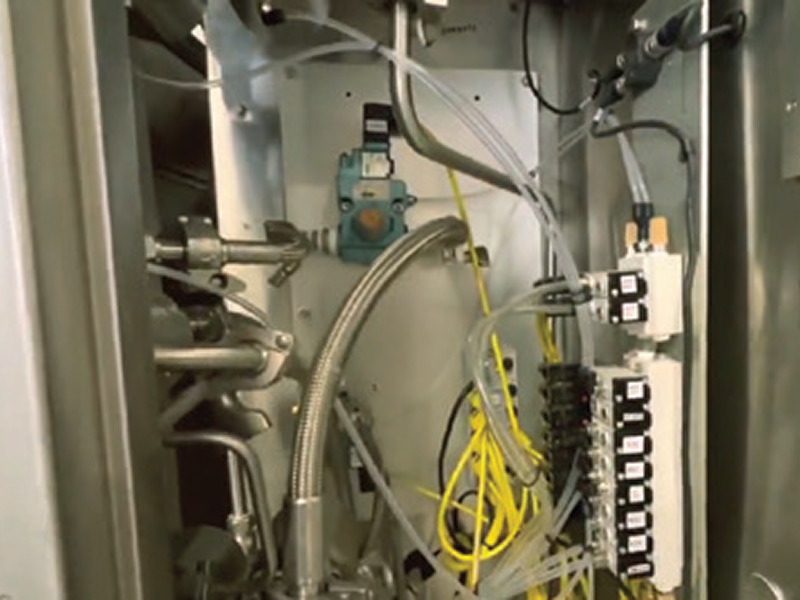
Pneumatic System
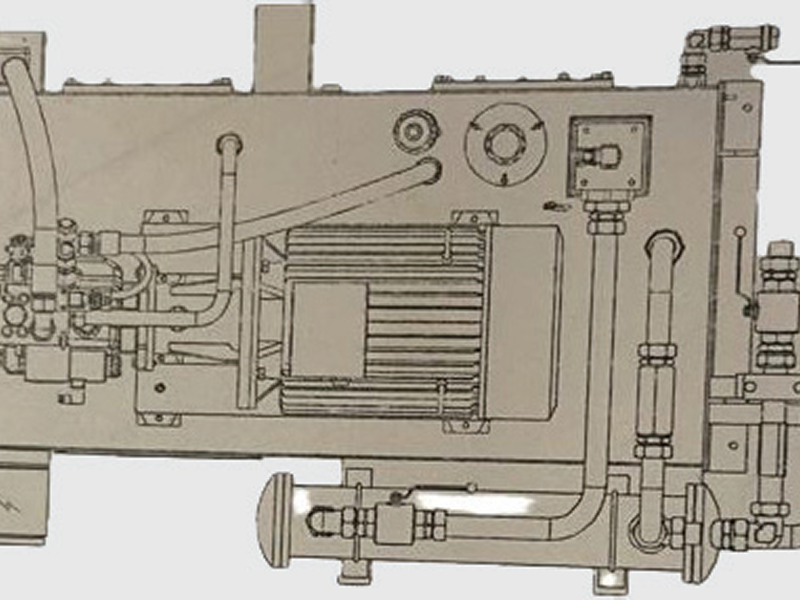
Hydraulic System
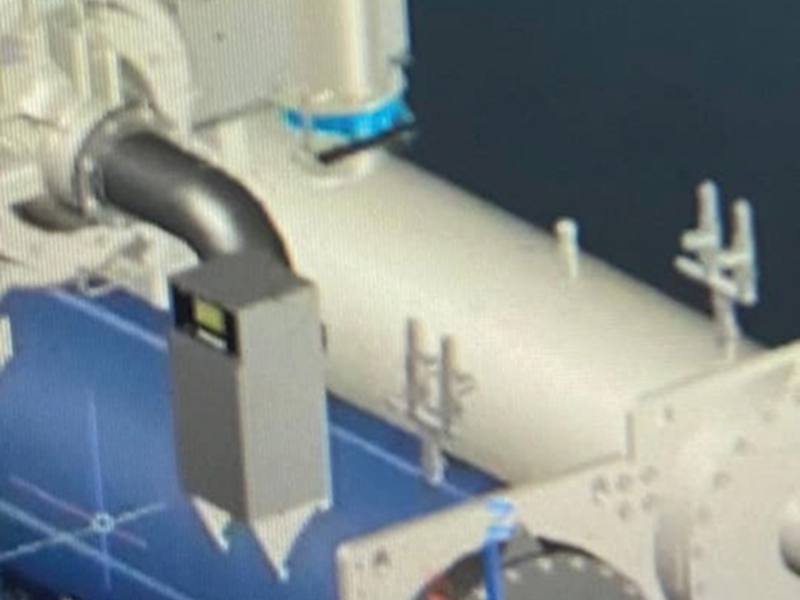
Water Cooling System
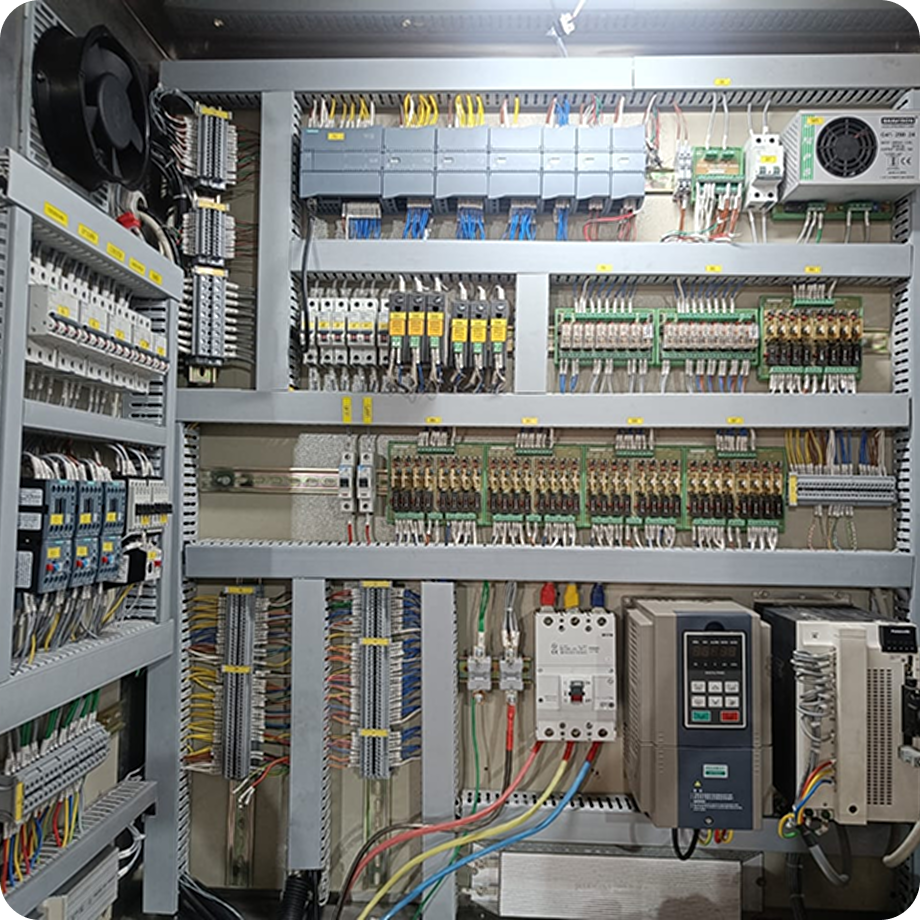
Control Panel & Diagnostics
Our Solutions
Comprehensive Troubleshooting Guidelines
Quick and practical solutions to common BFS challenges, ensuring seamless operations and minimal downtime.
Flaw | Solution |
---|---|
General flaw in Mould | Sand blasting |
Mould Seal Leakage | Tip & Joint Alignment |
Bottle falling problem during mould opening | Check overcutting |
Hanger cutting | Check closing point pressure |
Solution dropping problem | Check TPD |
Hydraulic related problem | Check the pressure |
Parison thickness & length | Adjust the parison head mechanical setting |
Filling volume variation | Check valves & timers from buffer tank up to Filling section |
Batch failure due to contamination | Online particle counter monitor across the Filling section |
Irregularity in bottle neck for euro-capping | Neck section vacuum leakage |
Plastic leakage in parison head | Check Heating |
Extruder section plastic movements | Check heaters/barrel cooling & temperature sensors |










BFS Solutions for your Industry Application
Delivering Blow-Fill-Seal systems tailored to meet the unique needs of pharmaceutical and packaging industries worldwide.
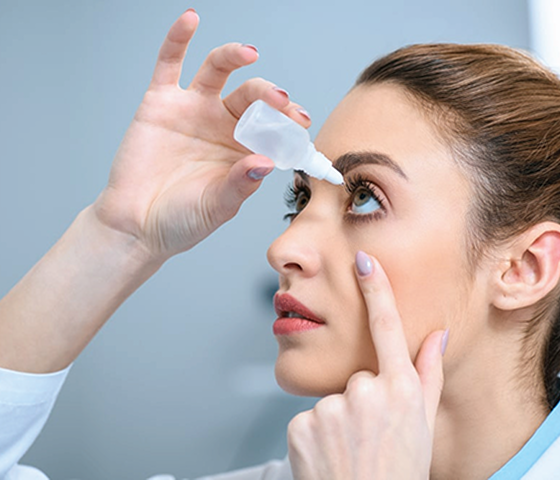
Ophthalmics
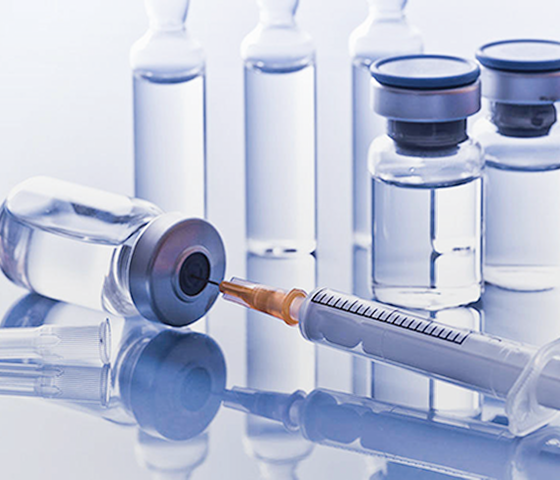
Injectables
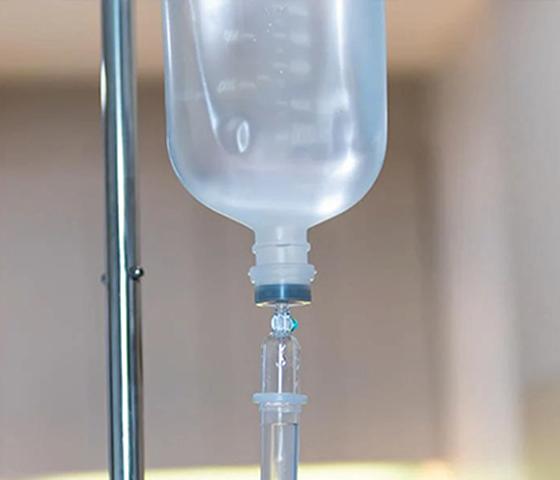
Infusions
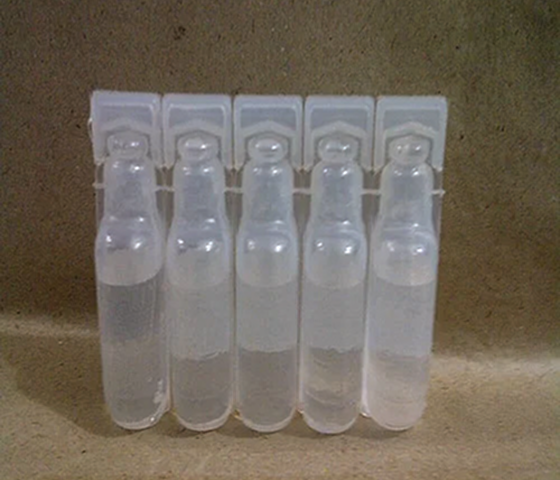
Inhalation Solutions
Our Testimonials
Listen from our Overseas Satisfied Clients
Hear firsthand from those who trust us with their health, well-being, and business.
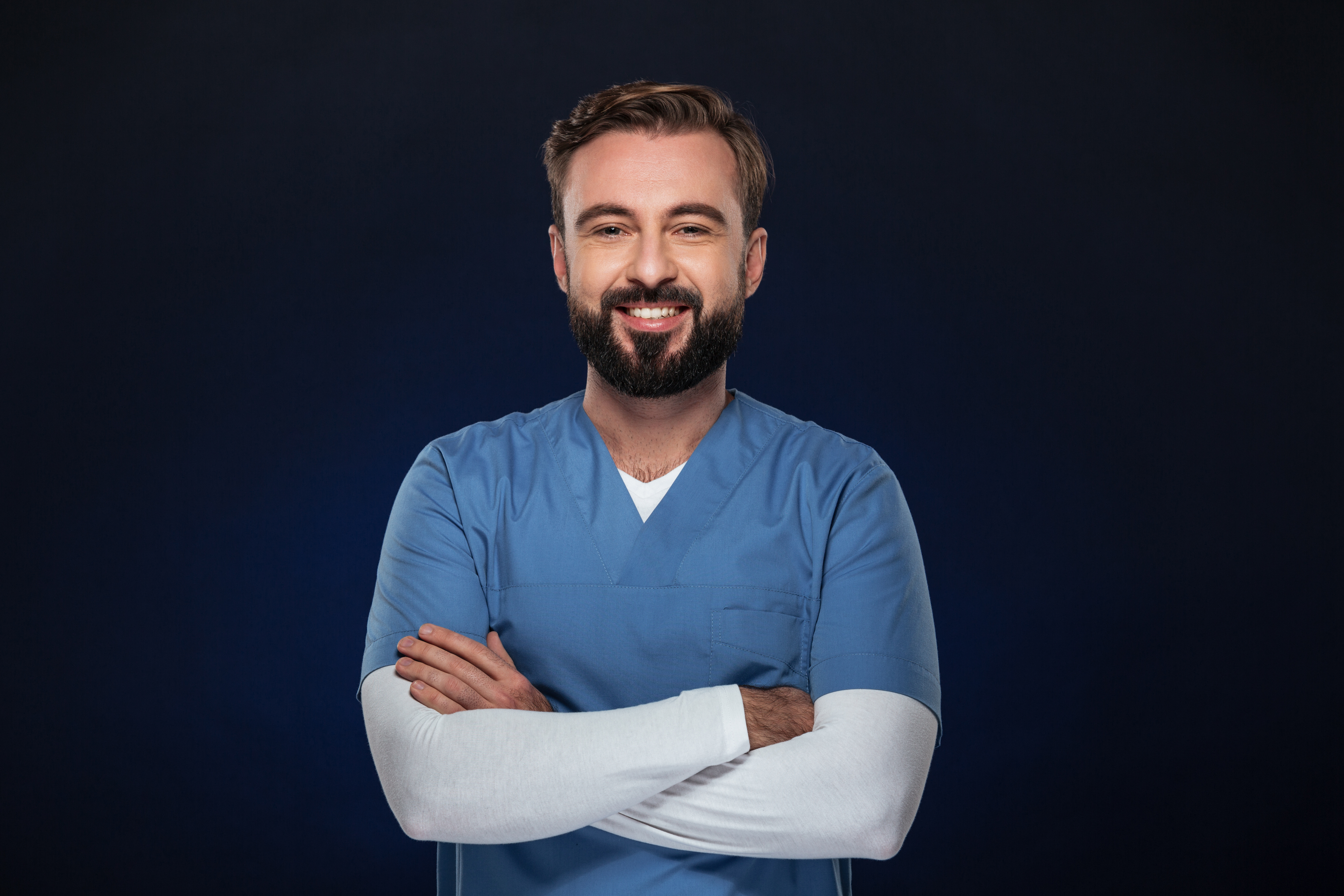
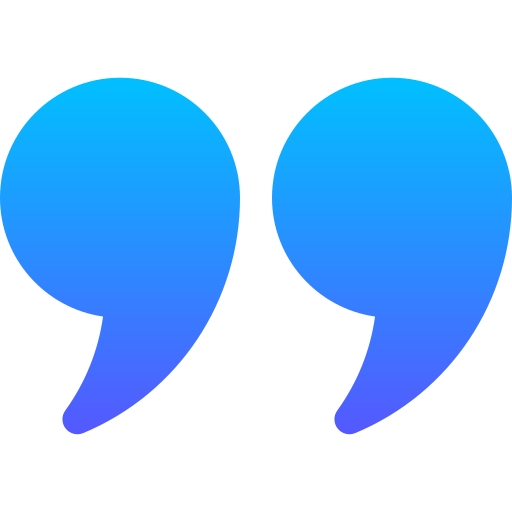
"V S Pharmatech's BFS machines revolutionized our production process. The quality and support are unmatched. Their dedication to excellence is truly commendable."
Michael Turner
FAQ's
Frequently Asked Questions
Find answers to your most common questions about our services and products.
BFS technology is an advanced aseptic processing technique in which plastic containers are formed by blow/vacuum, filled and sealed in one continuous process.
Our BFS containers are made from Low-Density Polyethylene (LDPE) for flexibility and chemical resistance or Polypropylene (PP) for higher temperature resistance and durability. Both materials are biocompatible and suitable for aseptic pharmaceutical packaging.
We ensure product sterility through aseptic BFS machines operating in low-particle environments, using protective air showers and pre-sterilized filling liquids. The container polymer undergoes high-temperature sterilization during the molten extrusion stage.
-Mould Chain (Rotary Machines): Relubricate chain elements.
-Mould Opening Cam (Rotary Machines): Relubricate for smooth operation.
-Mould Tool (Rotary Machines): Relubricate centering pins.
-Mandrel Unit: Replace O-rings on connection piece holder, mandrel, hood, insert, and shaft.
-Mandrel Hood Interlocks: Clean V-guides and guides.
-Connection Block: Replace guide bushes and guide rings.
-Aseptic Valves: Replace membranes and sealing discs.
-General Machine Lubrication: Ensure all lubrication points are serviced.
-System Checks: Inspect mould cooling lines, vacuum leakage, hydraulic pipe oil leakage, hydraulic oil level, extruder gearbox oil level, and extruder V-belt tension.
By putting the inserts in the mould, one can alter the objective volume. Example: 500ml without changing the change parts, one can fill 250ml for LVP by introducing the inserts. For SVP, one can go from 5ml to 20ml by introducing the inserts.